A Guide to Chemical Recycling
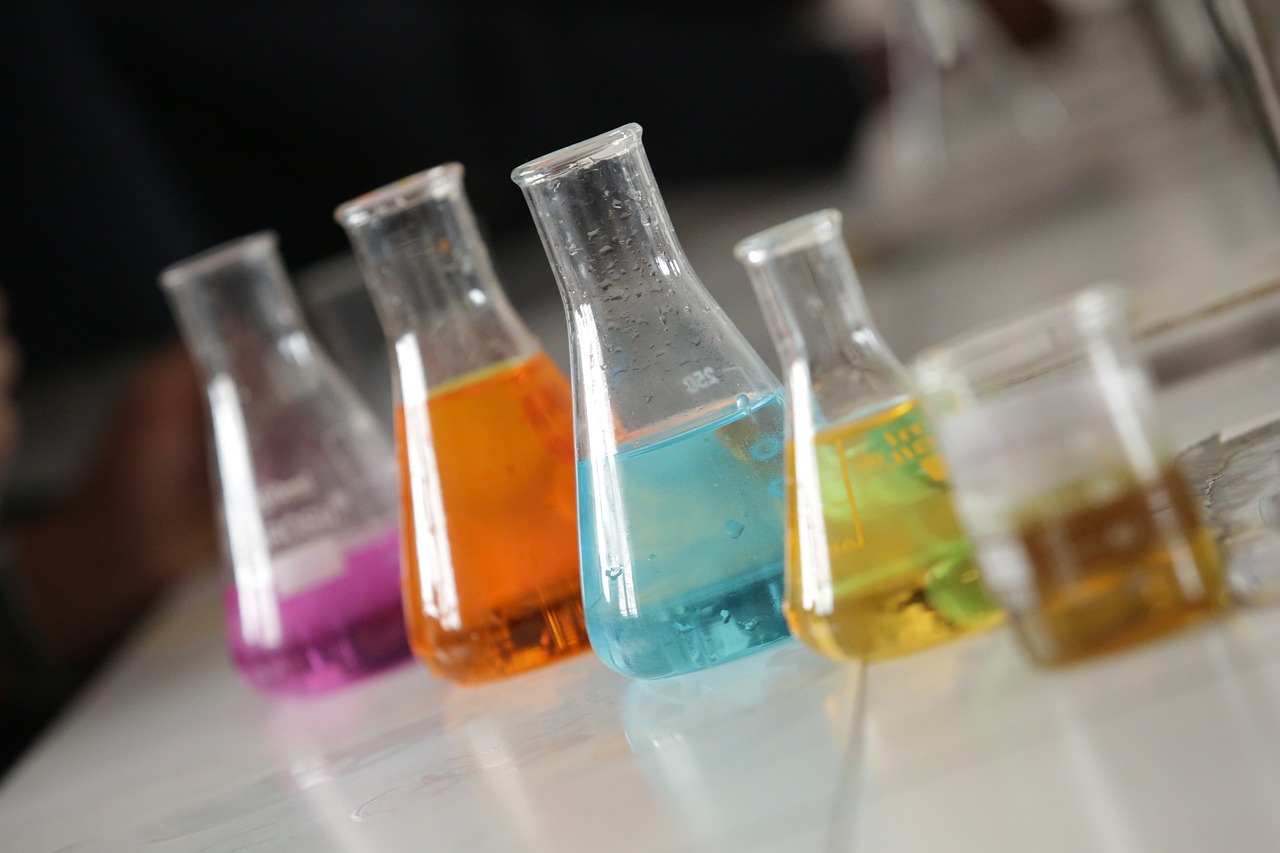
Image by deepakrit from Pixabay
Awareness as to the harmful effects of plastic on the environment is ever increasing. Along with this awareness comes initiatives to explore and develop new ways and techniques to process plastic waste to help create new materials for reuse.
Traditional recycling methods come with many challenges, typically related to what types of plastic can be recycled in the first place. Often, recycling facilities differ depending on location and that means recycling can be inconsistent.
As the environmental footprint of producing new plastic is high, both businesses and governments are looking at new ways that goods can be manufactured in a way that reduces this footprint.
Some of the initiatives include adapting the way certain materials are made or used, while introducing newer more environmentally friendly materials that avoid fossil fuels (such as crude oil).
Recycling and collection rates are another important focus area, so that more plastic materials are able to be processed and reused. In fact, the plastic collection rates are perhaps the most problematic aspect of the plastic waste epidemic since so little material is collected in the first place, in comparison to the amount of materials that are produced.
Finally, the introduction of new technology to deal with the plastic waste that is collected is also being developed. One such technology is called ‘chemical recycling’.
What is Chemical Recycling?
Chemical recycling is an advanced recycling process that focuses on converting polymeric waste at the molecular level, back into raw materials that can then be reused to manufacture new goods and products.
Often, this transformative process is used to deal with plastic waste and rubber, but it should be noted that not all polymers are plastic. For example – cotton can be used to make polymers and this is an organic material.
What is a polymer? Polymer means ‘many parts’ and these break down into monomers (single parts).
A polymer is a chemical compound, which has its molecules arranged in chains. Specific plastics (for example) are formed by chains of different types of polymers strung together. So, when we talk about chemical recycling for plastic, we’re referring to a recycling process that tackles polymers. Since these are the building blocks for plastic when a polymer is recycled so is the plastic waste.
Plastic pollution is escalating and to tackle this issue new recycling methods are being introduced to help improve plastic waste management. The goal of chemical recycling is to break down plastic waste into its base chemicals or plastic feedstocks so that these materials can be reused.
One of the key differences between chemical recycling and mechanical recycling is its ability to deal with more problematic plastic types. For example: polyethylene, polypropylene, and polystyrene which are very difficult to recycle (and therefore often not recycled) can be processed using chemical recycling methods.
Chemical recycling therefore offers the potential for overall improvements in recycling rates, extending the value of plastic materials past their normal lifecycle.
One of the key things to understand about chemical recycling is related to the end product that is produced. There are two broad categories of products that chemical recycling produces. The first is new base materials that can be reused for manufacturing into new products (such as plastic), and the second, perhaps more controversially – is as fuel.
To get a thorough picture of how chemical recycling works it is useful to understand how traditional plastic recycling is undertaken.
Understanding Mechanical Recycling
Mechanical recycling is the traditional way that plastic materials are dealt with in the recycling industry.
The general process for traditional mechanical recycling firstly involves sorting the plastic waste into its various types and colors so that it can be processed. Then the plastic is cleaned and contaminants such as labels are removed. Once the plastic is ready for processing, the material is then shredded into small plastic fragments. After the plastic fragments have been processed, they are then further washed and dried, before being melted and reformed into plastic pellets. These plastic pellets are then used to create brand-new products.
A couple of the biggest problems with mechanical recycling is the fact that it can only accommodate certain plastic types. Mechanical recycling is used to recycle polyethylene (PE), polypropylene (PP), and polyethylene terephthalate (PET). The difficulty in recycling PE, PP etc. is not that the plastic is hard to recycle, more that it comes in so many different forms, which use a wide range of chemical additives, which will effect the final performance of a product.
Not only is mechanical recycling ‘pickier’ in terms of the types of plastic it can process, but the bigger issue, and one that will also affect chemical recycling is that regardless of recycling schemes and recycling programs that any given country has implemented, the majority of plastic waste doesn’t get recycled. As Statista highlights, less than 10% of plastic is recycled each year, leaving a whopping 90% of plastic that has the potential to be processed, ignored, and left to be burnt or deposited in landfills, or worse still, the environment.
Ultimately, as Trucost note, the actual cost of recycling plastic and reusing it can be less than the cost of producing virgin material depending on market conditions such as the level of Shale gas production.
The Different Types of Chemical Recycling
The first thing to note about advanced recycling or chemical recycling is that it is not just one process, there are several different ways chemical recycling can be carried out, so the term chemical recycling is a catch-all phrase that covers a few different technologies.
Conversion technologies are used to transform one material into another state. In the realm of chemical recycling this is to break down plastic materials back into their basic chemical components so that they can be further processed to make new materials. For example, three such technologies that are classified as conversion technologies are pyrolysis, gasification, and depolymerization, and these in turn all fall into the chemical recycling category.
Pyrolysis is a method that converts waste plastics into reusable materials by heating the waste to high temperatures to break down the polymer chains that form the plastic. This heating process turns the polymer chains into simpler hydrocarbons. Pyrolysis is a process of heating without oxygen, which breaks down the materials into smaller molecules which can then be converted into another useable resource such as gas (typically, standard incineration uses oxygen to burn).
The process of pyrolysis creates pyrolysis oil which can be used as feedstock to produce new plastic materials. The industrial pump manufacturer Milton Roy says that this new feedstock accounts for around 25% of the output, whilst the rest of the material is converted to fuel or char (ash that can be used as a building material). Pyrolysis can create three main substances, solid char, liquid bio-oil, and combustible gases.
Gasification also uses heat to convert a substance (in the case of the plastic industry, plastic waste) into a gas (syngas) which is then sold commercially as fuel. There is an argument that this is not much better than incineration since the materials that are used to create syngas are not recycled into reusable plastic materials, breaking the circular economy.
The technology involved in gasification is somewhat better than simple incineration but it still comes with its detractors. While gasification can also capture C02 (helping with climate change targets) turning plastic into fuel will still contribute to climate change when that fuel is used so it is not necessarily an ideal solution to the plastic problem.
Hydro cracking is a technology that has been around for a while and has been used in the petrochemical industry to convert hydrocarbons into products such as gasoline and diesel. In the remit of plastic waste, hydrocracking is used to break down the hydrocarbon polymers present in plastic waste into valuable products such as fuel.
Depolymerization is a chemical recycling process that is designed to break down polymers into smaller, more useful molecules. The process of depolymerization is used to produce monomers that can then subsequently be used to manufacture new polymer products.
Advantages of Chemical Recycling
Chemical recycling offers many benefits, that both go to addressing some of the environmental concerns we have with plastic, along with providing some valuable economic opportunities for those who invest in the process.
Perhaps the first advantage of chemical recycling over traditional recycling methods is the fact that it can process a much wider variety of plastic waste. Often, plastic materials that are currently destined for landfill or the incinerator can be dealt with via the chemical recycling process. For instance, some colored plastics, mixed-material plastics, and certain plastic types can be processed. This means that the overall plastic waste recycling rate is increased when chemical recycling is used.
Another benefit that chemical recycling has over mechanical recycling is its ability to deal with mixed plastics and contaminated plastics. This is often a big problem for the recycling industry, but the chemical recycling process can handle this more effectively. This again, helps improve recycling rates since fewer materials are discarded.
The quality of the plastic materials that chemical recycling produces is much improved over mechanical recycling, and this can match even the quality of brand-new, virgin plastic. This means that plastics that are formed from the chemical recycling process can be used in difficult and sensitive applications where virgin plastic is typically used. For example, in the food and pharmaceutical industry.
Increased recycling rates mean that there is potentially a reduced reliance on virgin fossil resources. Therefore, the carbon footprint associated with materials made from the chemical recycling process is lower than it would be if creating new plastics.
However, it should be noted that since our dependence on plastic is increasing and therefore the need for raw plastic materials is higher, regardless of whether it is virgin or recycled the overall carbon footprint of the plastic industry as a whole is going up.
New technologies such as chemical recycling have a role to play in the circular economy since they help reduce the need to create new, raw materials by creating a pool of plastic feedstock that can be used to make new products.
Chemical recycling contributes to waste minimization by converting old materials into new materials that can be reused. Since the chemical recycling process can tackle unrecyclable plastic waste and convert it into petrochemical feedstock it keeps the material in use for longer than it would be if it was just discarded into a landfill.
Challenges Facing Chemical Recycling
Chemical recycling on the surface looks to be a great method to help combat plastic waste, especially for the more problematic plastic types that would traditionally not be recycled and therefore go to waste. However, as with most things the process of chemical recycling isn’t perfect and isn’t a miracle solution to the plastic problem.
Chemical recycling comes with certain challenges, some unique to the chemical recycling process itself, and other issues that traditional recycling already faces.
Chemical Recycling isn’t necessarily a ‘clean’ technology. A report by NRDC highlights some of the issues with chemical recycling which includes the creation of hazardous waste as a by-product of the conversion process.
The toxic waste created by chemical recycling plants are often carcinogens and neurotoxicants, such as benzene and lead which is known to be harmful to human health. Often this waste is subsequently incinerated which adds to the pollution and climate change problem.
Chemical recycling uses energy to process materials, which can increase carbon emissions, more so the case when the source of that energy is fossil fuels. On the plus side, the process is much more efficient than traditional incineration but still creates more greenhouse gas emissions than if the plastic was simply dumped in a landfill.
Plastic contamination is a problem for both chemical recycling and mechanical recycling. Contaminates ultimately mean that the plastic wastes need to go through cleaning processes before being used in the recycling plant.
The other issue with chemical recycling is the output of the process typically creates more fuel stock than new plastic materials. One of the criticisms of environmental groups is that the chemical recycling process is more like a form of incineration rather than a recycling facility and therefore is more akin to energy recovery initiatives.
Another problem is that chemical recycling produces much lower yields than mechanical recycling for like-for-like materials. This means that mechanical recycling is still the preferred method for dealing with plastic types that can be easily processed using this method.
There is some debate, especially from environmental groups as to whether chemical recycling is actually classified as recycling and therefore can be allocated against recycling targets using approaches such as mass balance. In Europe, for example, campaign groups have asked the European Commission to rethink the current rules for certain types of plastic such as PET where chemical recycling competes with the more efficient mechanic recycling methodology.
As with mechanical recycling one of the main issues is the supply of suitable feedstock to the industry. No matter how good chemical recycling technologies may be, if there isn’t a comprehensive and sufficient collection and sorting process in place in the supply chain then there will not be enough materials to scale the industry.
Perhaps the final challenge facing chemical recycling is that it is still an emerging market and is effectively still a small-scale technology when compared to mechanical recycling with just a few plants in comparison to mechanical recycling facilities. There are plans and incentives to make this technology large-scale since it is considered a valuable way to expand the ability to recycle content and tackle certain waste streams that would otherwise be neglected.
While the commercial scale of chemical recycling is on the increase the positive environmental impact is still very small especially when considering the majority of the plastic waste processed by chemical recycling is converted into fuel and not new plastic materials. Considering the much lower yield rates that this method of processing offers this further reduces the potential for this method to positively impact the environment, at least in the near future until the industry is significantly upscaled.
These challenges do highlight the complexity and difficulty facing the chemical recycling industry as a real solution and alternative to mechanical recycling or our continuing reliance on plastic production.
The Future of Chemical Recycling
Ultimately, chemical recycling is not the complete solution to the plastic waste epidemic, but is instead another tool that can be used in the fight against plastic pollution. The benefits that chemical recycling can offer for the reprocessing of certain plastic types are very important when compared to some of the limitations of traditional plastic recycling methodologies.
While governments and the chemical industry believe that chemical recycling may play an important role in the plastic recycling process and for sustainability it is not without its problems. These issues aside, it is generally considered by legislators and industry that it is still better to process plastic using the chemical recycling method as opposed to simply dumping plastics into landfills or incinerating them inefficiently.
Businesses and investors are also taking note, and money is being allocated to chemical recycling initiatives since the ability to recycle challenging plastic materials that would otherwise be incinerated or end up in landfills, offers a potential lucrative revenue stream as the technology further develops. However, some plants have been operating at significant losses due to the cost of the entire process involved. Ultimately, it is still much more cost-efficient to make virgin plastic rather than recycling and reuse the materials.
Chemical recycling investment in large territories such as the European and the American market offers massive opportunities to not only reduce plastic waste deposits that are entered into the environment but also is an economically attractive proposition.
Learn about The Plastic Collective
The Plastic Collective works to tackle the plastic waste problem through plastic reclamation projects and initiatives, along with facilitating plastic reduction with plastic audits along plastic credit schemes for businesses.
Sign up for our plastic offset program to help your business become plastic neutral. Learn more about becoming plastic neutral at Plastic Collective.